As a supply chain organization, would you agree that these are the two prime concerns lying at the heart of every asset-intensive unit’s functioning?
The above concerns revolve around the maintenance of overall ideal equipment effectiveness. Particularly if an organization comes from the mining, power and utilities, oil and gas, or chemicals industry, the concern is loud and clear. Ensuring unmatched equipment uptime and minimized 'break-fix' costs of these assets is neither a cakewalk nor a rocket-science module, as long as organizations are prepared to embrace the technology at hand.
Many legacy organizations are still working with solutions that aren’t quite up to today’s challenges and use cases. Their manual systems do not utilize the data to make more holistic decisions - incurring costs on maintenance, and leading to loss of productivity due to unplanned asset failures. Hence, there is a need for accurate and reliable asset management driven by automation, digitalization, Industry 4.0, and the Industrial Internet of Things (IIoT) brought together on the floor.
Equipment reliability, as a part of Asset performance management, can be established via systems that boast off of advanced IoT solutions that enable anytime, anywhere, and any type of asset monitoring.
It is no new knowledge that equipment maintenance is becoming more complex day by day. And this is why asset-intensive organizations need to absolutely work smarter to improve their equipment uptime and also be able to reduce their operating costs at the same time.
So, how does the mountain move?
· Work with optimized business processes that increase enterprise value.
· Remote monitoring, specialized analytics, and predictive maintenance.
Operational excellence with Real-time Asset Tracking
Manufacturing/shop floor and/or warehouse organizations can unlock the ‘smart’ in themselves when they truly are able to capture the location of assets, objects, vehicles, and goods. By tracking inventory, spare parts, operations supply, production equipment, and indoor vehicles in production areas, unplanned activities can be minimized to quite an extent. By tracking and sharing reliable location data of assets with the right people and applications at the right time, expensive delays unnecessary downtime, and misuse of the workforce can be put to check.
Talking of applied benefits…
Detect, identify, and avoid performance degradation or asset failures.
The result - improved asset utilization and availability, improved safety, reduced MRO (maintenance, repair, and operations) spend, improved return on assets, and improved operational performance.
Asset Utilization that works smarter
Asset management can be drastically improved by enabling intelligent actions and decisions at the field level. To put it simply, the smart way is to process industrial assets information as close to the asset as possible, by delivering critical information at the earliest. In this manner, the response time to enable machinery can be reduced.
The asset’s utilization score can be affected by factors that lead to the failure of the machinery running at its full capacity. Factors such as downtime, holidays, operator breaks, reductions in production because of seasonal demand are a few from the many factors contributing to the same.
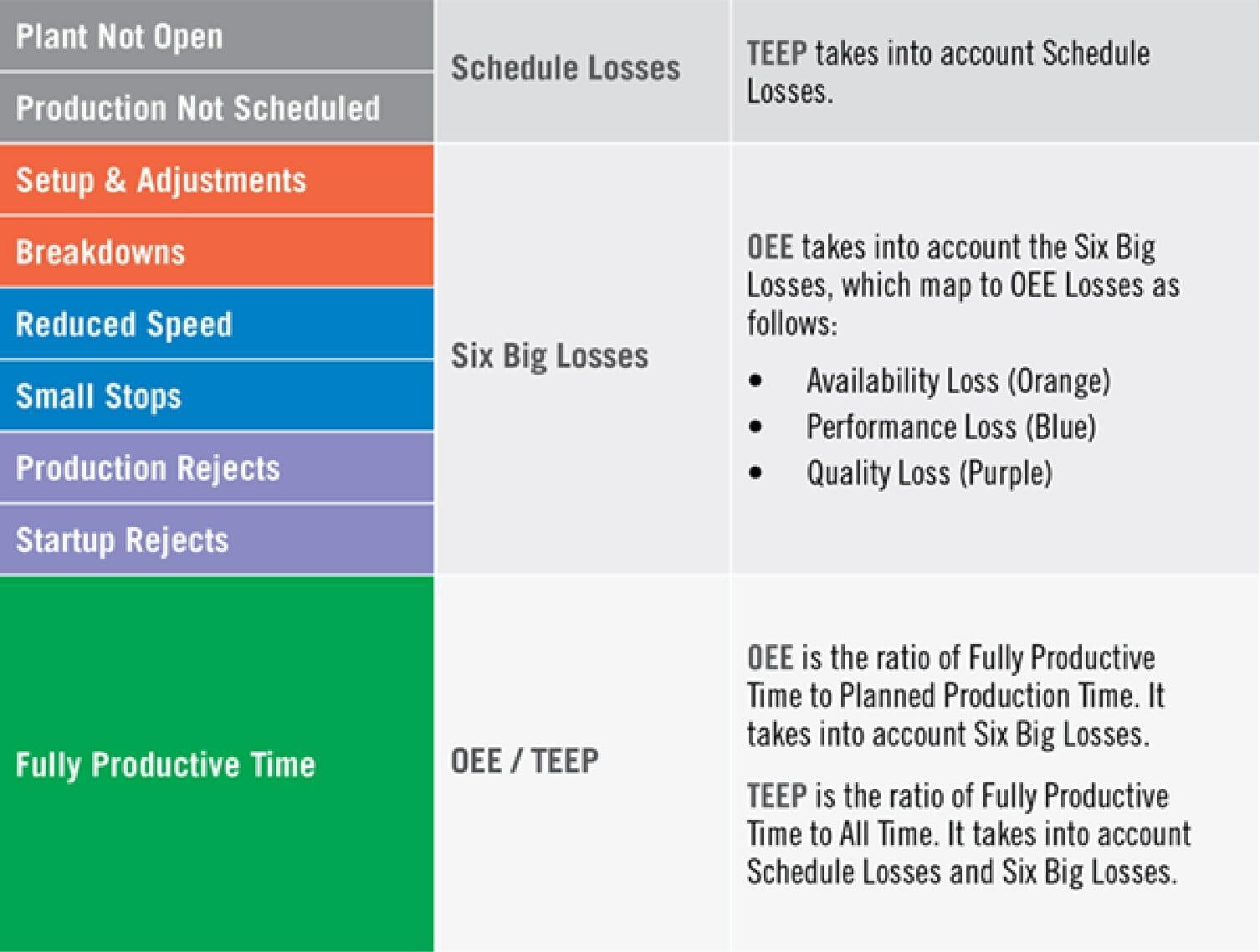
When an asset, as a resource, is utilized to its capacity, per-unit costs see a dip, the money frozen in surplus inventory is freed up, and the machinery is obviously utilized to its fullest. If that is not the scenario, prepared to be faced with the wrath of competitiveness and dwindling profitability.
The key to tackling Asset utilization blues is to work with utmost visibility into what’s causing asset deployment interruptions. And this is where ‘accurate data’ can help precise the utilization rate. Integration with IoT applications with other organizational data not only provides real-time visibility but also makes it easier to identify issues in machine availability, performance and job quality that may affect performance.
The prowess of predictability, actionable data, and next-generation Asset Performance Management
When organizations are capable of using advanced analytics, they get into the position of predicting issues before they happen. By interpreting the data garnered from IoT devices, advanced analytics, sensors, etc., manufacturing organizations can easily manage their asset performance. With actionable data at hand, the equipment uptime is maximized, and failures negated to the very least.
In a nutshell, when organizations choose to implement the ‘smart’ functioning of their operational tasks, they empower their systems and assets to function at optimum capacity, reduce maintenance costs, achieve marginal improvements in performance, increases in production, and enjoy the much-anticipated growth.