Overview
Because customers are consistently seeking products with extensive customizations and manufacturers are feeling pressure to mass-produce cost-effectively, it's critical that the integration of business and manufacturing systems occur with automation technology. In the past, these systems would operate separately. However, factories are becoming developing full integration and embracing connected manufacturing, so they can approach everything from sales to delivery confirmations more efficiently while simultaneously reducing costs.
What is Connected Manufacturing? - New integrated world
When looking at connected manufacturing, this business strategy explicitly leverages cloud computing as a means of harnessing business and operational data to gain greater control, customer satisfaction, efficiency, and visibility. You achieve end-to-end control and visibility when your people, processes, and supply chains have these connections.
Why is Connected Manufacturing Beneficial?
The use of a paperless system with full automation would improve not only efficiency but also reduce much of this manual work. The use of technology would create real-time connections throughout the manufacturing floor, as well as with other internal and external business systems. Another benefit to the use of this data is its potential for visual conversions, thus allowing all employees to understand and analyze the information efficiently.
The Possibilities for Connected Manufacturing - Manufacture at scale
Inventory tracking
No longer is guesswork part of tracking inventory thanks to automated inventory tracking. There is the possibility of a significant increase in efficiency, as well as a reduction in errors.
Manufacturing products
It's possible to create a manufacturing line of "connected" products. For example, these products could contain sensors to collect and display information to consumers, thus improving their experiences.
Real-time tracking
When products experience real-time tracking, it's possible to receive a full set of data as it moves throughout the production line. These efforts help manufacturers understand the logistics and determine where improvements are necessary.
How Can Manufacturers Use These Benefits to Their Advantage?

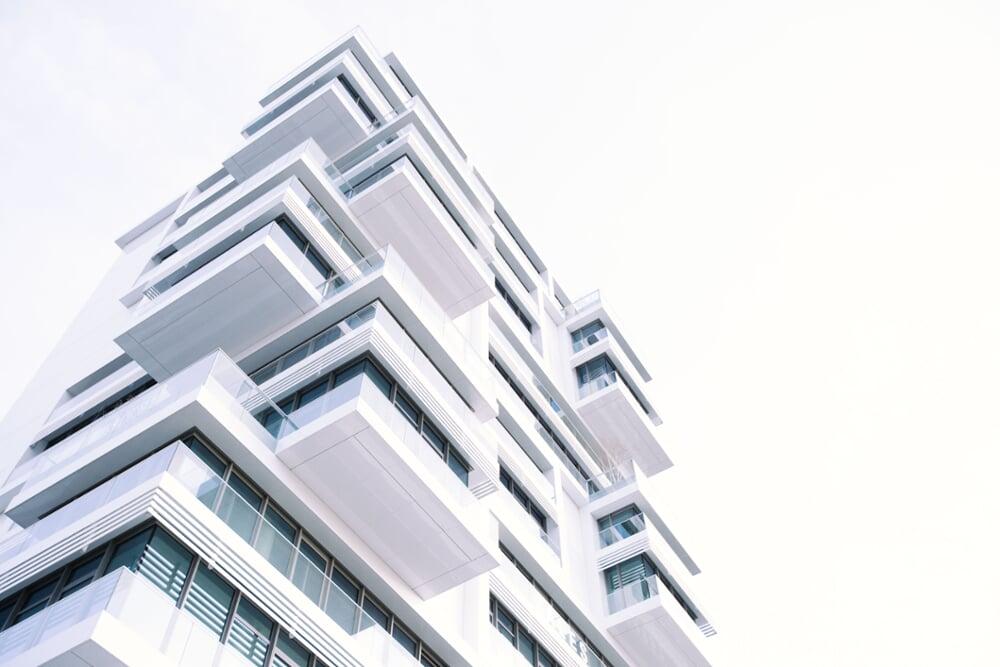
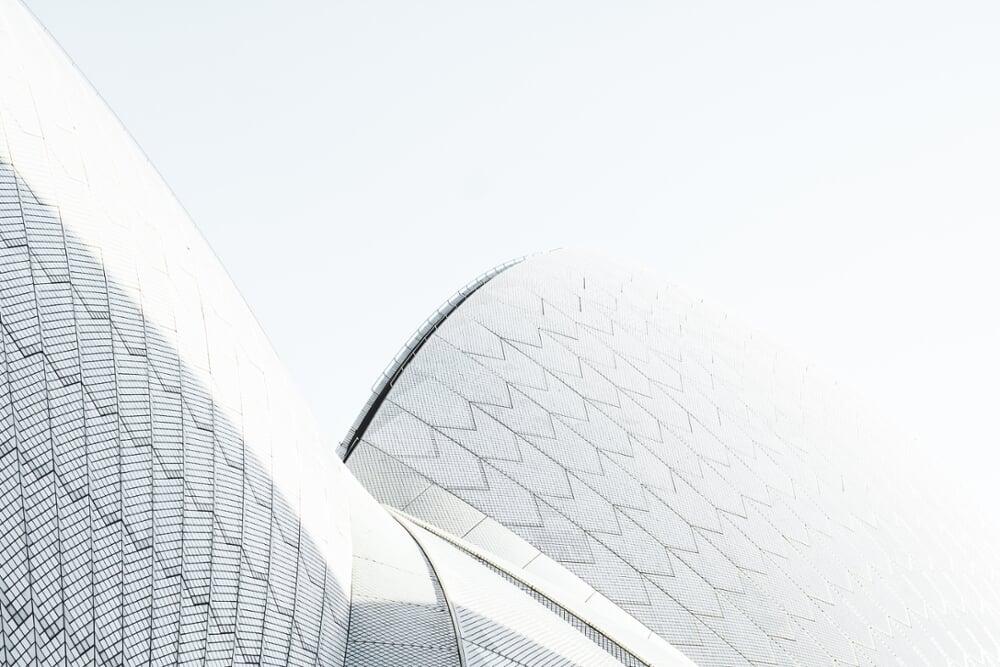
Why Connected Manufacturing?
The longer you wait to embrace connected manufacturing, the further behind your company will be behind the rest.
The more you learn about this way of integration, though, the better chance you'll have at embracing this business strategy.
Rather than experiencing errors or down-times, or other frustrations on the production floor, it's better to make adaptations with the shifting manufacturing industry.